Do I need a vacuum chamber for resin?
You can get great results with resin casting without investing in specialized equipment like a vacuum chamber. Vacuum chambers are primarily used to remove air bubbles from resin, but they’re not a necessity for every project. Many factors influence whether or not you need a vacuum chamber, including the type of resin you use, the complexity of your project, and your desired level of detail. For example, if you’re making jewelry or small crafts, the bubbles might not be as noticeable. However, if you’re casting larger pieces or working with intricate details, a vacuum chamber can be a valuable tool.
If you decide to skip the vacuum chamber, there are a few simple techniques that can help you minimize air bubbles. These include:
Mixing your resin slowly and thoroughly: This helps to avoid trapping air bubbles in the mixture.
Pouring your resin in a thin stream: This allows the air bubbles to escape more easily.
Using a heat gun or torch to gently warm the resin: This can help to release any trapped air bubbles.
Letting the resin sit for a few minutes before pouring: This gives the bubbles time to rise to the surface.
You can also add air release agents to your resin, which help to eliminate bubbles by breaking the surface tension. With a little practice, you can create beautiful, bubble-free resin creations even without using a vacuum chamber.
How to degas epoxy resin?
Here’s how to degas epoxy resin:
You’ll need a vacuum chamber and a container for your resin. First, mix your epoxy resin as you normally would, but remember, this step is really important – you need to leave enough headspace in the container for the resin to expand. The container should have at least three times the original volume of the resin. Now, place the container with the mixed resin inside the vacuum chamber. Pull a vacuum to about 29 inches of mercury. This will remove air bubbles from the resin, resulting in a smooth and strong final product.
Now, let’s break down why this is so important! Air bubbles in epoxy can create a few problems:
Weak spots: Air bubbles can weaken the final product, creating weak spots and potentially making it more likely to crack or break. Think of it like a tiny hole in a piece of cloth – it weakens the fabric!
Uneven finish: If you’re using epoxy for a project like a tabletop or a piece of jewelry, those air bubbles can create an uneven, unsightly finish. Imagine a perfectly smooth, glossy surface, but then you have those little bumps and blemishes from the bubbles. It’s not ideal!
Reduced durability: Air bubbles can also make your epoxy project less durable over time. That smooth, shiny epoxy might become cloudy or brittle because of the tiny air pockets trapped inside.
So, what happens during degassing?
When you pull a vacuum, you’re essentially creating a low-pressure environment inside the chamber. This low pressure forces the air bubbles trapped inside the resin to expand and rise to the surface. The vacuum pulls them out, leaving you with a beautifully degassed, bubble-free epoxy resin! It’s like magic, but it’s actually science!
A few things to keep in mind:
Different resins may have different degassing requirements. Check the manufacturer’s instructions to ensure you’re using the correct vacuum pressure and time.
Don’t overdo it! Degas for too long, and you might risk evaporating some of the resin’s volatile components.
Use a good vacuum pump. A strong pump will create a deeper vacuum, leading to better degassing and a smoother, stronger finish.
I hope this helps! Happy degassing!
Can you use a hair dryer to get bubbles out of resin?
Here’s how a hairdryer can help:
Heat: The heat from the hairdryer can help the bubbles expand, making them easier to pop. You can think of it like how a hot air balloon works.
Movement: The hot air from the hairdryer can also create movement in the resin, which can help the bubbles rise to the surface. It’s like giving them a little nudge.
Remember, a hairdryer isn’t a magical bubble remover. You still need to follow some best practices to make sure you get the best results:
1. Mix your resin properly: This is the most important step. If your resin isn’t mixed properly, it won’t cure correctly and you’ll be more likely to have bubbles.
2. Pour your resin slowly: Pour your resin slowly and carefully to avoid introducing air bubbles.
3. Use a heat gun carefully: A heat gun can be more effective than a hairdryer, but use it carefully to avoid overheating the resin.
And here’s the most important tip: Patience is key! Give the resin time to settle and the bubbles to rise to the surface before you start using a hairdryer or a heat gun. You can try using a toothpick to gently pop any stubborn bubbles that are still lingering. It might take some time, but if you follow these tips, you’ll be able to create beautiful, bubble-free resin projects.
How to get rid of air bubbles in resin?
Here are some popular methods:
An artist’s torch, heat gun, kitchen torch, or even a lighter can be used to gently warm the surface of the resin. This encourages the bubbles to rise and pop.
A toothpick or straw can be used to carefully poke at the bubbles, helping them to release.
Just remember: You’ll want to keep a close eye on your resin over the next few hours. Sometimes, those little bubbles can reappear! If you see new bubbles forming, you can repeat the process of gently warming or poking them.
A few tips for success:
Use a slow-moving resin: Slow-moving resins give you more time to work and reduce the chances of air bubbles forming in the first place.
Avoid over-mixing: Over-mixing can actually introduce more air bubbles.
Pour in layers: If you’re working with a larger project, pour the resin in layers to give it time to settle between each pour.
Use a vacuum chamber: If you’re a serious resin artist, a vacuum chamber can be a valuable tool for removing air bubbles. It creates a vacuum that sucks the bubbles out of the resin.
Getting rid of air bubbles might seem like a little detail, but it can make a big difference in the clarity and finish of your resin projects! With a little patience and the right tools, you can create beautiful, bubble-free pieces.
How to make a vacuum pump at home?
First, you’ll need a syringe. Carefully burn a hole into the syringe using a heated knife. You’ll then need to screw a valve into that hole. Next, cut a piece of plastic tubing and slide it over the syringe’s top. Now, insert the non-threaded end of another valve into the tubing. Finally, attach a tube of any length to the threaded end of the valve you just inserted.
And that’s it! You’ve successfully made a simple vacuum pump!
How it Works
The vacuum pump you’ve built is based on a simple principle. When you pull back on the syringe plunger, you create a low-pressure area within the syringe. This pressure difference causes air to be drawn in from the attached tubing. This is similar to how a vacuum cleaner works, but on a much smaller scale.
The valve you screwed into the syringe acts as a one-way door. It allows air to enter the syringe when you pull the plunger, but prevents air from escaping when you push the plunger back in. This is crucial for creating and maintaining a vacuum.
Important Things to Remember
* This method is best for demonstrating how vacuum pumps work, rather than for serious applications.
* The valves are crucial for this project. You can use valves from old bike pumps or even repurposed components from other devices.
* You can experiment with different tubing sizes to see how it affects the suction strength of your pump.
Remember, safety should always come first. Be careful when working with hot objects. If you’re not comfortable with the process, you can always find other ways to learn about vacuum pumps. But if you’re up for a fun and educational experiment, this homemade vacuum pump is a great way to get started!
Why is a vacuum chamber necessary?
Imagine you’re designing a spacecraft. You need to make sure that the materials you use can withstand the extreme conditions of space, which includes a near-perfect vacuum. How can you test this on Earth? A vacuum chamber is the answer. By creating a vacuum inside the chamber, we can simulate the conditions of space and see how materials react.
This is just one example. Vacuum chambers are used in many different industries, from aerospace to electronics, and they’re essential for a wide range of applications. They are used for:
Testing the effects of a vacuum on materials: This can help engineers choose the right materials for specific applications, like designing satellites or medical devices.
Simulating space conditions: Vacuum chambers are used to test the performance of spacecraft components and systems before they are launched into space.
Degasification: Removing dissolved gases from materials, which is crucial for making high-quality products.
Thin-film deposition: This process involves coating materials with a thin layer of another material, often used in the production of electronics.
Sputtering: A process used to deposit thin films of materials onto a substrate.
These are just a few of the many applications for vacuum chambers. Their versatility makes them an indispensable tool in many industries.
Can resin cure without air?
This is because the curing process is a chemical reaction between two parts: Part A and Part B. The magic happens when these two parts mix, and they don’t need air to react. All they need are the right chemical components. Think of it like baking a cake – you don’t need air to make the batter rise, you just need the right ingredients and a little heat.
Here’s a little more detail about why this happens:
Epoxy resins are made up of molecules that have reactive groups. When Part A and Part B are mixed, these reactive groups start to connect and form long chains, creating a hard, solid material. This process is called polymerization. Air isn’t involved in this reaction; it’s a chemical reaction between the molecules themselves.
So, if you’re working with epoxy resin and need to seal it for some reason, you don’t have to worry about it not curing properly. The resin will cure just fine, even in an airtight container. Just make sure you mix the two parts thoroughly and follow the instructions on the product packaging for the best results.
Can you use a pressure cooker to degas resin?
But can you use a pressure cooker instead? While a pressure cooker creates pressure, it’s not designed for degassing resin. Pressure cookers are meant for cooking food, which requires much higher temperatures than resin degassing. The high heat in a pressure cooker could damage your resin, potentially causing it to become cloudy or discolored.
Here’s the difference between pressure pots and pressure cookers:
Pressure pots are specifically designed for resin degassing. They use gentle, controlled pressure at room temperature.
Pressure cookers are designed for cooking food at high temperatures. They’re not safe for resin as the heat can cause damage.
If you’re looking to degas resin, investing in a dedicated pressure pot is the best option. It’s designed for this specific purpose and will provide the optimal conditions for creating beautiful, bubble-free resin pieces. You can find pressure pots in various sizes depending on your needs.
Remember, resin degassing is an essential step for achieving professional-looking results. It ensures your resin creations are clear and free of imperfections, allowing you to showcase the intricate details and vibrant colors of your artwork.
See more here: Do I Need A Vacuum Chamber For Resin? | How To Degas Resin Without Vacuum Chamber
How do you Degas a resin?
While a vacuum chamber is essential for this process, you don’t have to break the bank. You can find affordable options for smaller projects.
Here’s how it works:
1. Prepare your resin: Mix your resin according to the manufacturer’s instructions.
2. Choose your container: Pick a container that’s large enough to hold the resin and leave some headspace. Headspace is the empty space above the liquid. This space is important, as the resin will expand when the vacuum is applied. Make sure you have at least three times the original volume of your resin in headspace.
3. Place it in the vacuum chamber: Now, you’ll place your container of resin inside the chamber.
4. Pull the vacuum: The vacuum chamber will pull the air out, creating a lower pressure environment. You’ll want to aim for a vacuum of around 29 inches of mercury. This will force the air bubbles out of the resin.
Why is all this headspace important?
Think of it like this: imagine a balloon filled with air. If you try to squeeze all the air out of it, the balloon will get smaller. The same thing happens with resin. When you pull a vacuum, the air bubbles in the resin are compressed and try to escape. The headspace allows the bubbles to expand and escape more easily, without causing your container to overflow.
Important tip: After you’ve degassed the resin, don’t rush to pour it into your mold. Let the resin sit in the container for a few minutes to allow any remaining bubbles to rise to the surface.
Ready to try it out? Go for it! Vacuum degassing is a really effective way to ensure your resin projects turn out smooth and bubble-free.
Does vacuum degassed resin have air bubbles?
While vacuum degassing does a great job of removing air bubbles from the resin, the act of pouring the resin into the mold can still introduce some. This is because the resin can trap air as it flows, especially if it’s poured too quickly or if the mold isn’t completely filled. That’s why pressure casting is often the best option for achieving crystal-clear, bubble-free parts. The pressure helps force the resin into every corner of the mold, reducing the chance of air getting trapped.
Here’s a closer look at how vacuum degassing works and why it’s not a foolproof solution for completely eliminating air bubbles:
Vacuum degassing is a process where resin is placed in a vacuum chamber. The reduced pressure causes dissolved air to come out of solution and form bubbles that rise to the surface. The resin is then poured into a mold. However, the resin can still trap air bubbles during the pouring process, even if it’s been degassed.
Think of it like this: Imagine a glass of soda. If you shake the soda vigorously, you’ll create a lot of tiny bubbles. The bubbles will eventually rise to the surface, but you’ll still have some bubbles trapped in the soda. It’s similar with resin. Even after vacuum degassing, there may still be some tiny air bubbles trapped within the resin.
Why pressure casting works better:
Pressure casting forces the resin into the mold, squeezing out any trapped air. It’s like filling a balloon with water – the water pressure pushes out the air. Pressure casting can also help to reduce the formation of bubbles in the resin itself, as the pressure keeps the resin from expanding and creating pockets of air.
Here are some additional tips to help minimize air bubbles in your resin castings:
Use a slow, steady pouring technique. Avoid splashing or pouring the resin too quickly.
Make sure your mold is clean and free of dust. Dust and other debris can trap air in the resin.
Use a degassing chamber that is large enough for the volume of resin you’re using. This will ensure that the resin is fully exposed to the vacuum.
By following these tips and choosing the right casting method, you can create beautiful, bubble-free resin castings.
How do you vacuum Degas a resin?
Vacuum degassing is a crucial step in working with resin, especially when you want to ensure a bubble-free finish. It’s a pretty straightforward process, but here’s how it works:
Step 1: Pulling a Vacuum
You’ll need a vacuum chamber specifically designed for resin degassing. This chamber creates a low-pressure environment, pulling the air out of the resin. A typical vacuum level is 29 inches of mercury.
Step 2: Bubble Removal
As the air is sucked out, the bubbles trapped inside the resin rise to the surface. This is because the lower pressure in the chamber reduces the pressure holding the bubbles down. The bubbles then collapse, leaving a clearer, bubble-free resin.
Step 3: Time is Key
The process usually takes a couple of minutes. However, you’ll want to be mindful of the resin’s working time. Resins with short working times should not be vacuum degassed. If you vacuum degas for too long, you risk the resin becoming too thick and unusable.
Step 4: A Clear Result
When you remove the resin from the vacuum chamber, you’ll see a noticeable difference. The resin will appear bubble-free and ready for your project.
The Science Behind It
Think of it like this: imagine a soda bottle. When you open it, the pressure inside decreases, and bubbles rise to the surface. This is similar to what happens during vacuum degassing. The low pressure in the vacuum chamber allows the trapped air bubbles to escape, resulting in a smoother, more professional-looking finish.
Important Considerations
While vacuum degassing is an effective technique, it’s essential to understand the limitations. Some resins, especially those with additives or fillers, might not completely degas, even with a vacuum. Additionally, always follow the manufacturer’s instructions for your specific resin. These instructions will provide guidance on the appropriate vacuum pressure and degassing time.
Final Thoughts
Vacuum degassing is a simple yet powerful technique for creating high-quality resin projects. By removing air bubbles, you can achieve a smoother, more professional finish. Remember to use a suitable vacuum chamber, follow the recommended vacuum levels and degassing times, and be mindful of the resin’s working time for optimal results.
What is the difference between open pour and vacuum degassed resin casting?
The open pour method, as the name suggests, involves simply pouring the resin into the mold. This can result in hundreds of tiny air bubbles becoming trapped within the resin. These bubbles are often quite obvious in the final casting.
Vacuum degassed casting offers a significant improvement over the open pour method. In this method, the resin is placed under vacuum before being poured. This process removes dissolved air from the resin, leading to fewer air bubbles in the final casting. However, even with vacuum degassing, some air bubbles can still form during the pouring process.
Why does this happen? It’s all about the pressure difference between the resin and the surrounding air. When you pour resin into a mold, there’s a slight pressure difference between the resin and the air. This pressure difference can cause some air bubbles to form as the resin settles. This is especially true for resins that have a high viscosity, which means they are thicker and resist flow more easily.
Pressure casting, which involves pouring the resin into the mold under pressure, is a more advanced technique that can minimize the formation of air bubbles. This method forces the resin into the mold with greater force, reducing the opportunity for air bubbles to form.
In summary:
Open Pour: Simplest, but air bubbles are a major concern.
Vacuum Degassed Casting: Significantly reduces air bubbles but not always completely.
Pressure Casting: The most advanced method, delivering the fewest air bubbles.
Choosing the right casting method depends on your specific project and the desired level of clarity and finish in your resin castings. If you want to minimize air bubbles, vacuum degassing is a good place to start. And if you are looking for the absolute best clarity, pressure casting is the way to go.
See more new information: linksofstrathaven.com
How To Degas Resin Without Vacuum Chamber | How Do You Get Bubbles Out Of Resin Without A Vacuum Chamber?
Let’s face it, sometimes you just need to get your resin project going, and you don’t have a vacuum chamber handy. We’ve all been there. But don’t worry, there are ways to degass resin without that fancy equipment!
Why Do We Degas Resin?
First, let’s talk about why we degass resin at all. It’s a simple matter of bubbles! When you mix resin and hardener, tiny air bubbles can get trapped inside the mixture, which can lead to a few problems:
Cloudy Finish: Those bubbles make your project look hazy and uneven.
Weakened Resin: Air bubbles can make your cured resin weaker and more prone to cracking.
Uneven Appearance: The bubbles can create a bumpy, uneven surface.
So, how can we get rid of those pesky bubbles without a vacuum chamber?
Methods for Degas Resin Without a Vacuum Chamber
Here are some methods you can try:
1. The Stir-and-Wait Method:
This is the simplest approach, and it works surprisingly well for many projects.
1. Mix Your Resin: Follow the instructions for your specific resin brand.
2. Stir Thoroughly: Use a wooden stick or a spatula to stir the resin mixture for at least 2 minutes. Be sure to scrape the bottom and sides of your container to make sure all the resin is mixed well.
3. Let It Sit: Place your container of resin on a flat surface and let it sit for 15-30 minutes. The bubbles will rise to the surface as the resin settles.
4. Skim Off Bubbles: Gently skim off any remaining bubbles on the surface with a toothpick or a small piece of cardboard.
2. The Heat Method:
Heat can help to accelerate the release of bubbles.
1. Warm Your Resin: Place your resin container in a warm water bath (not boiling) for about 5 minutes. Make sure the water level is below the rim of the container.
2. Mix and Stir: Remove the resin from the water bath and mix it thoroughly.
3. Let It Sit: Let the resin sit for a few minutes to allow the bubbles to rise.
4. Skim Off Bubbles: Gently skim off any remaining bubbles on the surface.
3. The Vibratory Method:
Vibrations can help shake those bubbles out!
1. Mix Your Resin: Follow the instructions for your specific resin brand.
2. Vibrating Surface: Place your container of resin on a vibrating surface. This can be a small plate on top of a washing machine or an electric toothbrush. The vibration helps to release the trapped air bubbles.
3. Let It Sit: Let the resin sit on the vibrating surface for about 5 minutes. You can also try gently tapping the bottom of the container to further encourage bubble release.
4. The Pressure Method:
Pressure can also help to force the bubbles out. This method is particularly useful for epoxy resin, which is known for being more prone to bubbles.
1. Mix Your Resin: Follow the instructions for your specific resin brand.
2. Pressure Pot: You can use a pressure pot designed for resin casting or even a large pressure cooker (make sure it’s clean and dry!). Pour your resin mixture into a sealed container that can withstand pressure, like a jar with a tight lid.
3. Apply Pressure: Follow the instructions for your pressure pot or pressure cooker to safely apply pressure to the container.
4. Let It Sit: Let the resin sit under pressure for at least 30 minutes. This will force the air bubbles out.
5. The Air Injection Method:
While it’s not technically degassing, this technique can help to minimize bubbles before they form. It’s great for projects with a large amount of resin.
1. Mix Your Resin: Follow the instructions for your specific resin brand.
2. Air Injection: Use an airbrush or a syringe to gently inject a small amount of air into your resin mixture while you mix it. This creates small bubbles that will rise to the surface and burst, leaving fewer bubbles behind.
3. Stir Thoroughly: Stir the resin mixture for at least 2 minutes to ensure all the resin is mixed well and to allow any remaining bubbles to rise to the surface.
Important Considerations:
Resin Type: Some resins are more prone to bubbles than others. Epoxy resin, for example, tends to be more bubble-prone.
Ambient Temperature: Temperature can affect bubble formation. Warmer temperatures can make bubbles more likely to form. Try working in a cool, well-ventilated area.
Mixing Technique: Avoid stirring too vigorously, as this can introduce more air bubbles. Use a slow, gentle mixing technique.
Container Size: Use containers that are large enough to allow the resin to settle and the bubbles to rise to the surface.
FAQ:
Q: How long does it take to degas resin?
A: The degassing time varies depending on the method used. Stirring and waiting might take 15-30 minutes, while using a pressure pot could take 30 minutes or more.
Q: How can I tell if my resin is degassed enough?
A: You’ll know your resin is degassed enough when you don’t see any more bubbles rising to the surface. However, even if you’ve followed these methods, there might be a few tiny bubbles that remain. This is perfectly normal, and they will likely disappear during the curing process.
Q: What if my resin is still cloudy after degassing?
A: If your resin is still cloudy after degassing, you may need to use a different resin type, experiment with different degassing techniques, or consider using a sealant to minimize the appearance of bubbles.
Q: Can I degas resin more than once?
A: You can degas resin multiple times if necessary. Simply repeat the degassing process until you’re satisfied with the results.
Now that you know how to degas resin without a vacuum chamber, you can confidently tackle those resin projects, even without a specialized tool!
Degassing Epoxy Resin On The (Very) Cheap
All you need to do is pop a hole in the lid of your container, hold the device over the hole, and watch the magic. This method is great for anything smaller than a… Hackaday
How do you degassing resin without a vacuum chamber
You can degas resin without a vacuum chamber by using a pressure pot or mixing it thoroughly to release trapped air bubbles. Table of Contents. Understanding la-plastic.com
How to remove bubbles from resin castings with the vacuum
Most people would recommend a pressure pot for degassing resin. But if you use a slow setting resin, the vacuum chamber can really work on achieving crystal … YouTube
Bubble free pen blank (NO vacuum or pressure degassing)
Making a pen blank without using a pressure or vacuum chamber. I heated the resin and its bubble free.I am a proud member of makers media networkhttp://maker… YouTube
Removing Bubbles from Epoxy – EPO-TEK
This tip discusses three techniques for removing and re-ducing this entrapped air. Pre-mixed and frozen syringes are of Hg quickly. The key is to hold the vacuum for as short Epoxy Technology
Can/should I degas resin with a vacuum chamber? :
Yes you can vacuum degass your resin, and yes you should provided finances allow. Curing under pressure either shrinks the air bubbles physical size or forces the gas to dissolve into the resin, depending on Reddit
How to Pour Resin without Air Bubbles – Tips for Perfect Castings
How to degas resin without a vaccum Chamber? Firstly, it’s important to say that Urethane Resins are moisture sensitive, therefore bubbles found in cured urethane resin, are thecraftecademy.co.uk
Degassing Epoxy and Urethane Compounds – Crosslink
Urethane resins and hardeners should be protected from picking up moisture by applying a layer on Nitrogen on top of the material in the containers. Mixing urethane resin and crosslinktech.com
Vacuum Vs. Pressure When Resin Casting | Hapco, Inc.
Vacuum Degassing using the X-Vac™ Chamber. When placed under pressure, any air bubbles entrapped from the mixing and pouring process shrink to the point where they Hapco, Inc.
Is This The Secret To Bubble Free Resin Casting? No Pressure Pot Needed
How To Cast Bubble-Free Dnd Resin Dice Without A Vacuum Chamber Or Pressure Pot?!
5 Ways To Get Bubbles Out Of Resin | Resin Art
How To Remove Bubbles From Resin Castings With The Vacuum Chamber
But No Bubbles! Part 1
Diy Vacuum Chamber For Degassing Resin \U0026 Silicone
Removing Air Bubbles From Silicone Rubber Moulds Before Casting , No Expensive Vacuum Chamber
Link to this article: how to degas resin without vacuum chamber.
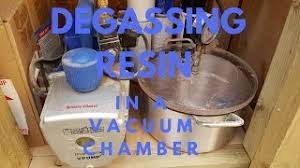
See more articles in the same category here: https://linksofstrathaven.com/how